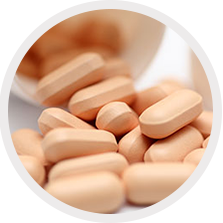
Analysis of the Whole Process of Dietary Supplement Tablet Production
I. Article Navigation
- Core Significance of Production
- Key Production Steps
- Formula Design
- Raw Material Selection
- Weighing and Mixing
- Compression Molding
- Coating Process (Optional)
- Quality Control
- Packaging Process
- Key Production Steps
- Production Challenges and Solutions
- Advantages of Tablets
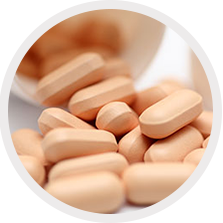
II. Core Significance of Dietary Supplement Tablet Production
The production of dietary supplement tablets is the process of transforming various nutritional components into a solid compressed form suitable for oral consumption. With the help of advanced equipment and strict quality control, it ensures that the products meet industry standards and provides consumers with a safe and effective way to supplement nutrition.
III. Key Production Steps
(I) Formula Design
- Combination of Nutrients and Excipients: Active nutritional ingredients such as vitamins are combined with excipients like binders to assist in shaping, improve taste and stability.
- Determination of Precise Proportions: Through research and experiments, the optimal proportion of each component is determined to meet the nutritional supplement needs.
(II) Raw Material Selection
- High-Quality Procurement: Obtain raw materials from reliable sources to ensure legal, traceable and compliant sources.
- Comprehensive Testing: Test the purity, safety and compatibility of the raw materials, and only use the qualified ones for production.
(III) Weighing and Mixing
- Accurate Weighing: Weigh each raw material with high precision according to the formula to ensure the accurate proportion of components.
- Thorough Mixing: Stir in professional equipment to evenly distribute the nutrients and excipients.
- Granulation Process (Optional)
- Wet Granulation: Add a liquid binder to form granules, then dry and screen them. It enhances the tablet strength but requires additional drying time.
- Dry Granulation: Directly compact the powder into granules, which is faster and suitable for water-sensitive ingredients, but the tablet strength may be relatively weaker.
(IV) Compression Molding
- Material Loading: Feed the processed material into the hopper of the tablet press.
- High-Pressure Compression: Use the tablet press to compress the material into tablets with specific shapes, sizes and hardness, taking into account both transportation and storage as well as disintegration in the body.
- Finished Product Ejection: The compressed tablets are automatically ejected for subsequent processes.
(V) Coating Process (Optional)
- Film Coating: Form a polymer film to improve the appearance and protect the nutritional components without affecting the dissolution in the body.
- Sugar Coating: Mask the unpleasant taste and make the tablets more palatable, suitable for specific groups.
- Enteric Coating: Allow the nutritional components that are absorbed in specific parts of the intestine or sensitive to gastric acid to be released in the intestine, improving the bioavailability.
(VI) Quality Control
- Weight Inspection: Ensure that the weight of each tablet is within the specified range to guarantee the accurate content of nutrients.
- Hardness Testing: Evaluate the ability of the tablet to resist breakage and ensure the appropriate hardness.
- Dissolution Test: Simulate the human body environment to measure the dissolution speed and degree of the tablet, ensuring the release and absorption of nutrients.
- Friability Test: Assess the resistance to abrasion to ensure the integrity of the tablet after transportation and storage.
(VII) Packaging Process
- Material Selection: Select suitable packaging according to the characteristics of the product, such as light-proof and moisture-proof blister packaging, to protect the product.
- Labeling: Clearly label the product information to facilitate consumers’ correct use.
IV. Production Challenges and Solutions
- Powder Flowability: The poor flowability of some nutritional powders may lead to uneven filling, etc. It can be optimized by improving the formula, adding glidants or upgrading the equipment.
- Tablet Defects: Cracks may occur during tableting and coating. It can be reduced by maintaining and calibrating the equipment, adjusting parameters and controlling the environment.
- Stability: Nutritional components are easily affected by the environment. Appropriate packaging, controlled storage conditions and stability studies can ensure the quality.
V. Advantages of Tablets
- Convenience: Small in size and easy to carry, can be taken at any time, suitable for the fast-paced lifestyle.
- Precise Dosing: The nutrient content is precisely controlled to avoid inaccurate intake.
- Good Stability: With a long shelf life under appropriate conditions, not easily contaminated and deteriorated.
- Wide Applicability: Can contain a variety of nutritional components to meet the health needs of different groups of people.
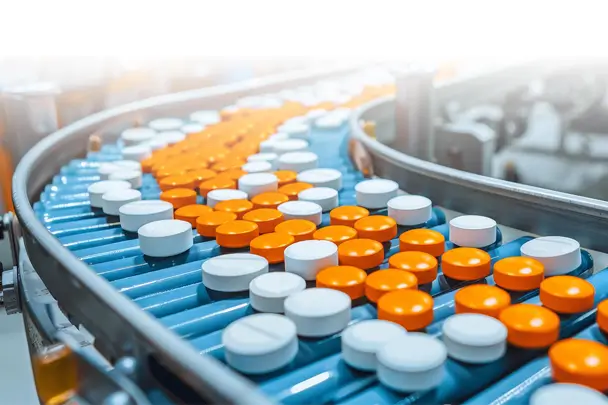